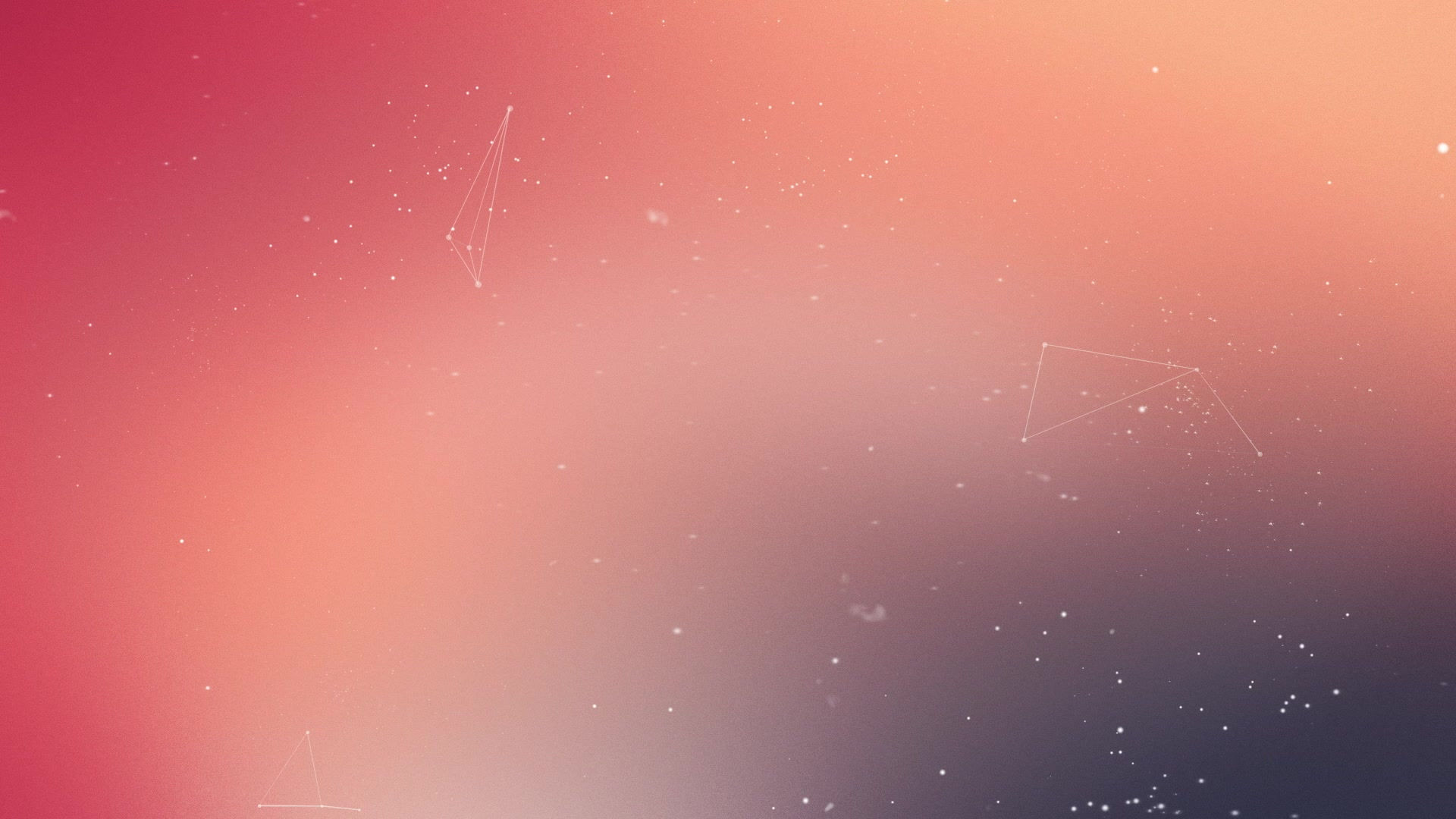
EAM Assessoria e Treinamentos no Processo Industrial e Segurança do Trabalho
Soluções de Problemas e Capacitação de Equipes
Noções básicas sobre Refino do Aço em Forno Panela da Aciaria
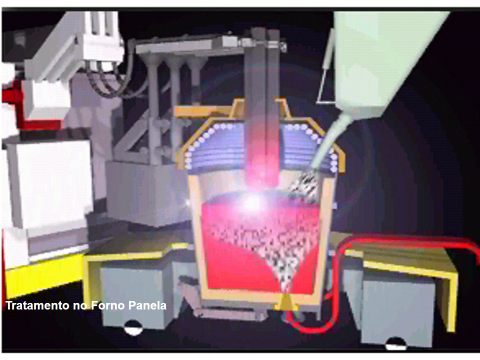
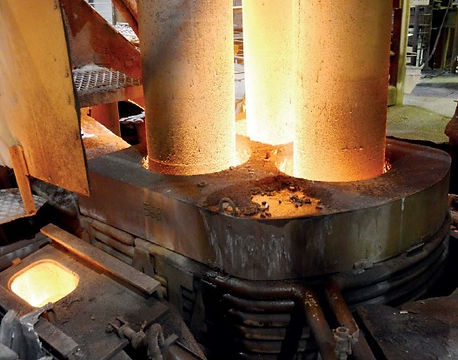
O Forno Panela é um dos equipamentos de extrema importância dentro do processo de uma Aciaria

A primeira unidade de Forno Panela no mundo teve início por volta de 1965. No Brasil, estes equipamentos foram introduzidos em 1969, mas a utilização evoluiu a partir da década de 80 do século XX.
No início, os Fornos Panela apareceram especialmente nas aciarias elétricas, produzindo aços de alta qualidade. O motivo era evitar os longos períodos de refino, que diminuíam a produtividade. Além disso, um ajuste estreito na temperatura foi se tornando uma necessidade primordial para o lingotamento contínuo de aços de qualidade, com alta produtividade.
O uso do Forno Panela também pode garantir o equilíbrio térmico entre o aço e o revestimento refratário da panela, que é um ponto chave para a qualidade. Em acréscimo, o lingotamento contínuo sequencial se tornou fator básico para fabricação de aços com alta produtividade, o que é facilmente alcançado usando o equipamento como um “pulmão” entre o forno primário (convertedor) e o Lingotamento Contínuo.
Outra razão importante é que, com o Forno Panela, há a possibilidade de reduzir o sobreaquecimento do aço líquido no forno primário, o que implica em aumento significativo na vida do revestimento refratário. Para se ter uma ideia, uma aciaria pode ter aumentada a sua produtividade em torno de 10 a 15% e, em alguns casos, alcançar 20% com a introdução de um Forno Panela.
Uma análise dos dados de instalações de processos de refino secundário existentes no Brasil, permite demonstrar que o forno panela é o tipo de processo mais utilizado no nosso país para a realização da etapa de refino secundário dos aços. Isto se deve em grande parte devido ao desejado equilíbrio entre os teores residuais de Al e/ou Si e o teor de oxigênio no aço líquido após o tratamento no refino secundário, justificando a maior popularidade dos fornos panela em relação aos processos de aquecimento químico. Deve-se levar em conta ainda que isto acontece apesar de, normalmente, o custo de instalação de fornos panela superar o custo necessário para a instalação de uma unidade de refino secundário por aquecimento químico.
As funções principais são:

Uma estação completa de refino secundário do tipo forno panela combina:
• Aquecimento do aço líquido por meio do calor gerado por um arco elétrico;
• Ajuste fino de composição química com adições de ferroligas, mesmo em grande quantidade.
• Injeção (borbulhamento) de gás inerte para agitação do banho metálico (utilizando lança e/ou plugue poroso);
• Injeção de arames (fios) recheados com compostos de Ca;
• Injeção profunda de pós de compostos de Ca (encontra-se desativado);
• Adição de escórias sintéticas para ajuste de composição (dessulfuração) e absorção de inclusões do banho líquido (troca e controle de escória);
• Adição de sucata canivete para correção de temperatura;
• Dispositivos para medição de temperatura do aço líquido;
• Dispositivos para coleta de amostras do aço líquido e da escória;
• Computadores de processo para monitoramento e controle das operações.
Desta forma, a estação cumpre basicamente as funções de:
• Efetuar ajuste da temperatura do aço líquido;
• Propiciar adequado sincronismo entre os convertedores e as máquina de lingotamento contínuo;
• Realizar a homogeneização de composição química e temperatura do aço líquido;
• Efetuar ajuste da composição química do aço líquido, inclusive com a
dessulfuração e a desoxidação do aço;
• Aumentar o rendimento das adições de ligas e alumínio devido à injeção de gases inertes para homogeneização;
• Permitir atender aos requisitos de faixas estreitas de composição química, devido à maior estabilidade nos rendimentos das adições;
• Possibilitar a flotação mais rápida das inclusões presentes no aço líquido e a absorção das mesmas pela escória (aumenta a limpidez do aço);
• Induzir a globulização de alguns tipos de inclusões presentes no aço (controle de morfologia de inclusões);
• A realização das adições sem a presença de escória também resulta em menor geração de inclusões devido à baixa reoxidação, contribuindo para o aumento da limpidez do aço;
• Em situações de emergência na aciaria, possibilita também, a retenção de corridas na panela por períodos de várias horas.
Facilidades de um Forno panela:
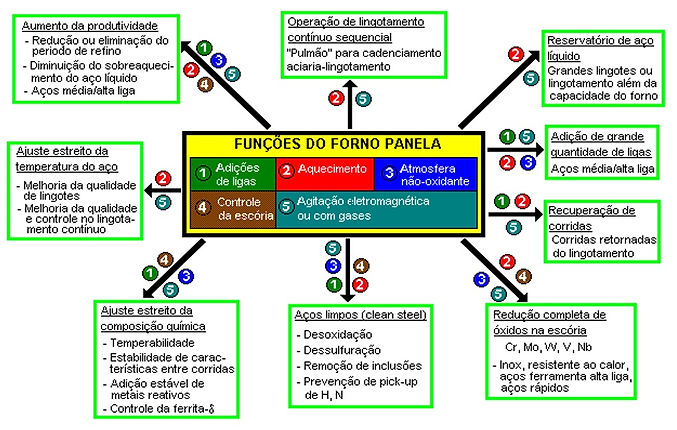
Representação esquemática dos principais componentes de um Forno panela:
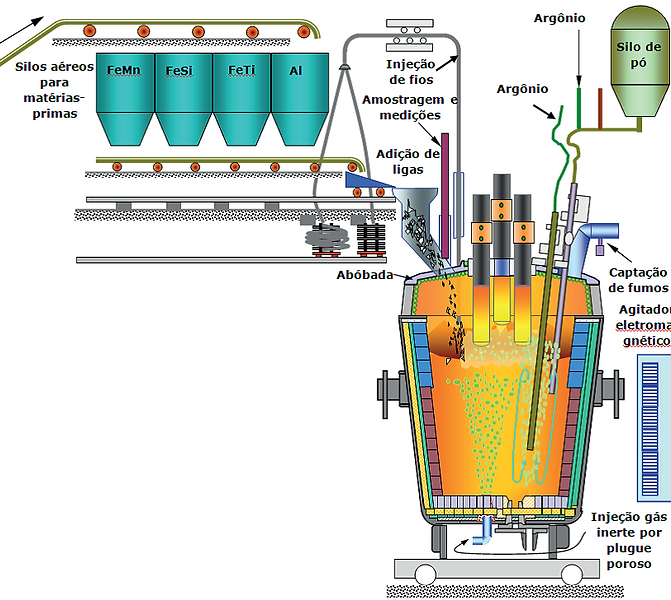
Basicamente este tipo de equipamento possui uma abóbada refrigerada a água (para minimizar o contato do aço com a atmosfera), um sistema de aquecimento elétrico com 3 eletrodos de grafite, plugue poroso e lanças para injeção de gás argônio. Existe ainda um sistema de adição de ferroligas e fundentes, equipamentos para retirada de amostras e medição de temperatura.
Ressalta-se que o Forno Panela não é exatamente um forno no sentido tradicional do termo usado, mas sim uma tampa equipada com eletrodos denominada abóboda, que durante a realização dos tratamentos de refino secundário é “acoplada” à panela.
Normalmente são utilizados três eletrodos em fornos de trifásicos de corrente alternada.
Os sistemas de adição de ligas e amostragens de temperatura e composição, dispositivos para agitação do banho com injeção de gases inertes ou equipamentos eletromagnéticos, sistema de captação de fumos e dispositivos auxiliares para deslocamento do carro porta-panela.
Geralmente as estações de Forno Panela possuem diversos equipamentos tais como:
• Carro panela;
• Abóboda móvel e refrigerada;
• Sistema de injeção de argônio por plugue ou lança;
• Medidor de borda livre automático (radar) ou não;
• Lança de temperatura;
• Lança de amostragem;
• Lança de argônio;
• Lança de pó;
• Máquina de injeção de fi os;
• Sistema automático de abastecimento de ferro ligas;
• Sistema automático de adição de ferro ligas;
• Sistema automático para troca de lanças de argônio e pó;
• Sistema de despoeiramento
O tempo total de tratamento em fornos panela varia de 30 a 70 minutos, dependendo das operações necessárias. Por exemplo, a utilização de dispositivos que minimizem a passagem de escória do forno primário para a panela, evita a operação de raspagem da escória remanescente e a perda de temperatura é reduzida. Nos aços de qualidade normal, não é feita a agitação para promoção da flotação de inclusões, economizando energia e tempo.
Para finalizar esse artigo, apresentamos um exercício simples para que seja possível ajudar no cálculo do tempo de aquecimento de uma corrida no Forno Panela nas seguintes condições:
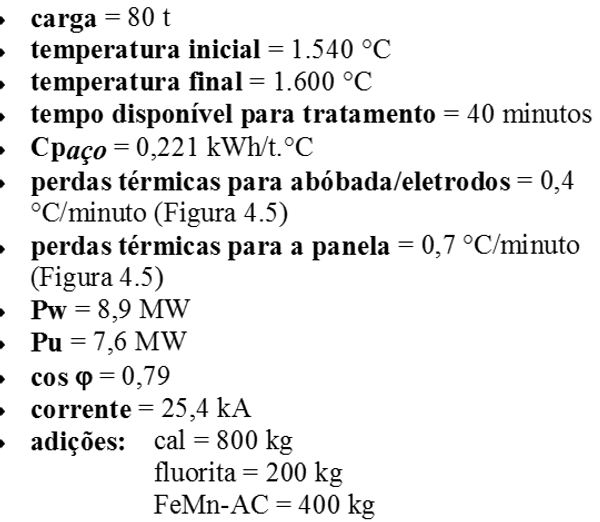

Conforme tabela de contribuição térmica de ligas e fundentes, temos:
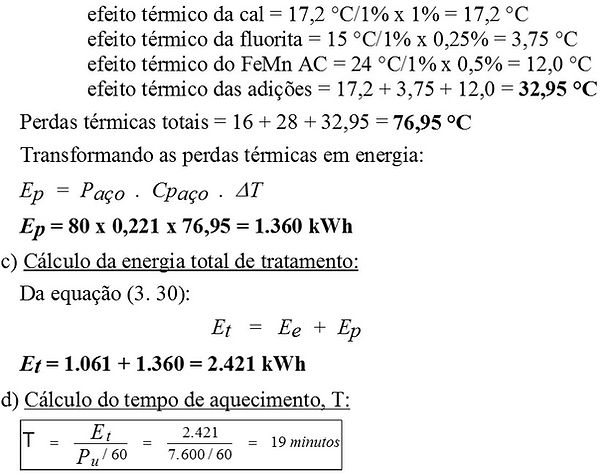
PRÁTICA DE AQUECIMENTO COM ARCO SUBMERSO EM UM FORNO PANELA DE 150 TON
1. Como se calcula o consumo de energia? Quais unidades são usadas?
Potência Elétrica (Watts) = Voltagem (Volts) * Corrente (I amperes)
Potência Elétrica = Potência (KW) * Tempo
2. Qual é o consumo (Kwh / ton.) para uma corrida de aço líquido normal e qual pode ser para uma corrida de aço líquido com baixa temperatura de chegada?
Transformador = 25 MVA = 25 MW
Eficiência = 90% 1 Kwh = 860 Kcal
Fator de potência = 80% Cp = 950 kcal / m3
25 mw x 0,90 x 0,80 = 18 Mwh
18 Mwh 1 hora 1000 KW = 300 KW
60 min 1 MW min
Para uma panela de aço líquido com 1550 ºC objetivando um aumento de temperatura para 1600 ºC
1 KWH 1000 W 3600 seg = 3 600 000 WS = Joules
1 KW 1 hora
1 cal = 4,186 Joules
X = 3 600 000 J X = 860,009.55 cal
1 cal = 0,0011612036 watts
Densidade do aço líquido = 7,019 ton / m³ (1000 kg / 1 ton) = 7019 Kg / m³
Q = m. Cp. Δ T = [(150000 kg * 7019 kg / m³) (950.000 cal / m³ ºC) (50ºC)]
Q = 5 x 1016 cal / 860 009.55 cal = 5.81 x 1010 cal = 67525098 watt = 67525 KWH
Se 67525 é de 100%; de 60 % = 40515.05 KWH