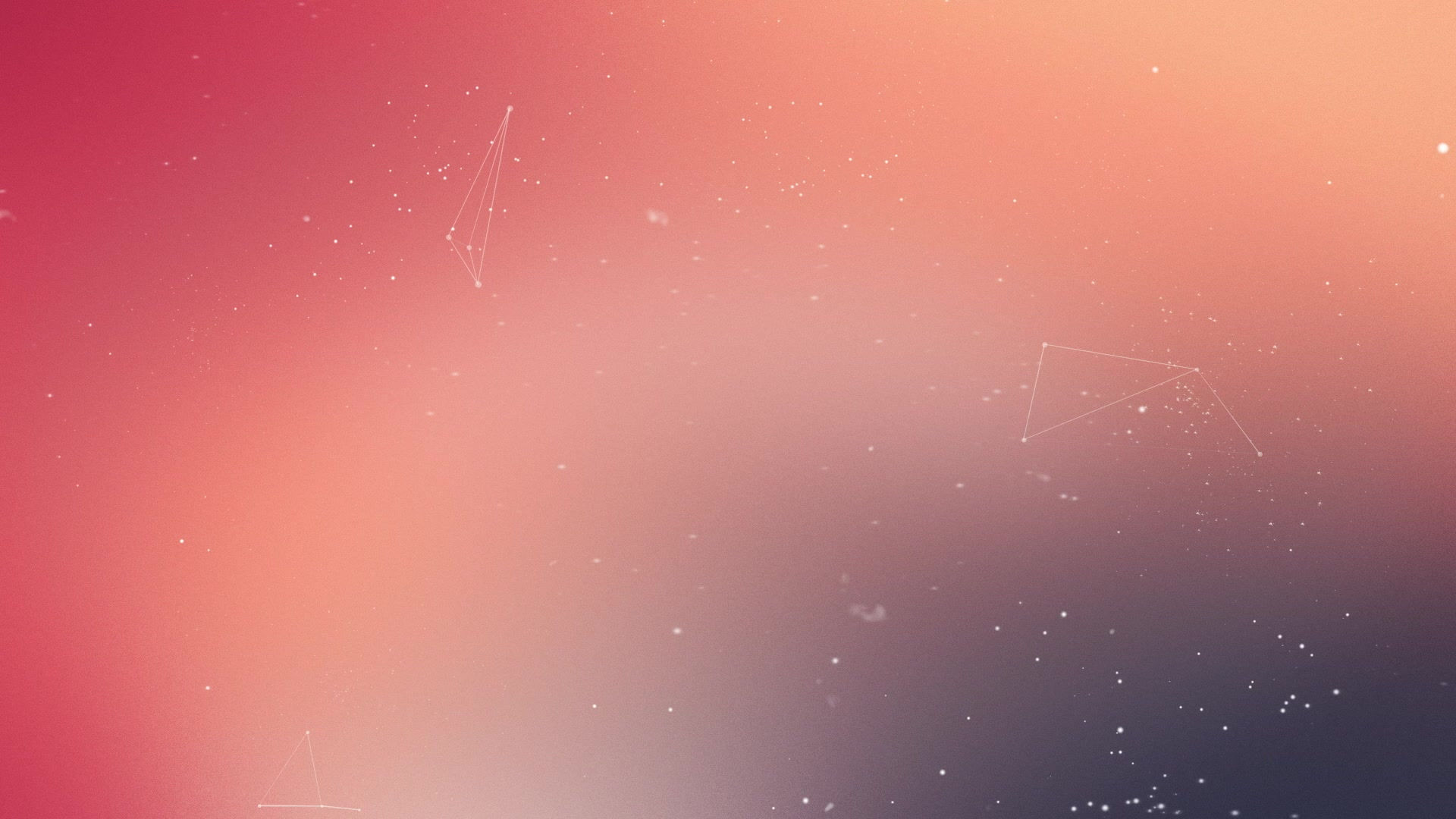
EAM Assessoria e Treinamentos no Processo Industrial e Segurança do Trabalho
Soluções de Problemas e Capacitação de Equipes
Circulação do aço líquido em um Desgaseificador à Vácuo RH
Breve Histórico do Processo RH
Em 1865, Henry Bessemer, pioneiro da produção de aço por processos pneumáticos, propôs a aplicação de pressões abaixo da pressão atmosférica para tratar o aço líquido na etapa de metalurgia secundária.
Na década de 50 do século XX, com o desenvolvimento dos sopradores de vapor, das bombas de vácuo e selada a água, os processos metalúrgicos com aplicação da técnica de desgaseificação a vácuo, tornaram-se possíveis.
Em 1955, surgiu o processo de desgaseificação no jato de aço líquido durante o vazamento, conhecido como processo SD (StreamDegassing), com objetivo específico de diminuir o custo elevado do tratamento de recozimento, provocado pela necessidade de aumento das dimensões dos lingotes usados como matérias-primas para o forjamento dos eixos de transmissão das usinas hidrelétricas.
Em 1956, foi apresentado o processo DH (Dortmund-Hörder Huettenunion) com apenas uma perna para subida e descida do aço para a câmera de vácuo.
O pesquisador A. Lorenz da Heraeus teve a ideia de efetuar a desgaseificação do metal líquido, método patenteado em 1957 na matriz da companhia Ruhrstahl Henrichshütteem Hattingen, o qual passou a pertencer ao grupo Thyssen.
Este processo foi posteriormente chamado processo RH, letras iniciais de Ruhrstahl e Heraeus, onde a câmara de desgaseificação possui dois tubos revestidos de refratários, um para entrada e outro para saída de aço, também de nominados snorkels, os quais são respectivamente chamados de perna de subida e perna de descida. As primeiras plantas de refino secundário a vácuo foram concebidas apenas para desgaseificação.
Os equipamentos utilizados no processo RH consistem em:
um vaso metálico revestido de refratário, com duas pernas na sua extremidade inferior e o sistema de vácuo conectado a sua extremidade superior, uma lança é inserida no interior do vaso, permitindo a injeção de oxigênio e de gás combustível para aquecimento.
Exite ainda, um sistema de adição de ferroligas e equipamentos para retirada de amostras, medição de temperatura e de teor de oxigênio.
Também são utilizados dispositivos para aquecimento do interior do vaso.


Taxa de Circulação do aço líquido no RH
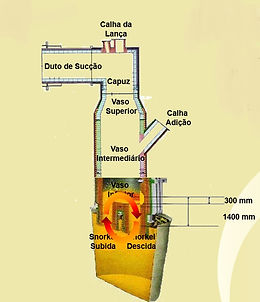

Os principais fatores que exercem efeito na eficiência do processo RH são:
• Profundidade de imersão das pernas do snorkel;
• Altura e diâmetro do vaso;
• Diâmetro das pernas do snorkel;
• Vazão de argônio na perna de subida;
• Pressão de trabalho;
• Composição inicial do aço (teores de oxigênio e carbono).
A profundidade de imersão das pernas do snorkel é o principal fator que controla o nível de aço líquido no interior do vaso. Baixas profundidades de imersão podem prejudicar a circulação do aço, além de proporcionar um maior desgaste da soleira do vaso durante o sopro de oxigênio. Dessa forma, objetiva-se a maior imersão possível para que se tenham a maior quantidade de aço no interior do vaso, o que permite:
• Maximizar a taxa de descarburação;
• Evitar arraste de escória para a parte superior do vaso;
• Evitar o desgaste do fundo do vaso inferior pelo jato de oxigênio.
Porém, deve-se ter um limite para esta imersão de modo a evitar transbordar aço da panela e atingir as partes não protegidas por refratário.
A subida inicial para penetração dos snorkels no banho deve ser feita de modo manual e visual.
A correção de altura após ligar o vácuo, pode ser feita de modo automático de acordo com a pressão interna e entrada dos estágios de ejetores, assim como a sua correção automática para descida da panela, antes do momento de desligamento dos ejetores para inundação do vaso.
O diâmetro do snorkel exerce forte influência na taxa de circulação, quanto maior o diâmetro da perna, maior a taxa de circulação de aço, porém, este é um dado de projeto, não sendo uma variável controlável durante o processo.
Este diâmetro pode ser alterado devido à deposição de inclusões (por exemplo, Al2O3) como resultado da utilização do aquecimento químico do aço (adição de Al combinada com a injeção de oxigênio) ou devido à projeção em demasia de massa refratária.
Na sequência, será apresentada uma tabela para simulação da quantidade de aço líquido que circula a cada minuto do processo entre uma panela de aço e interior de um vaso RH, através de uma equação utilizada para determinar a taxa de circulação em função de alguns parâmetros, dentre eles o diâmetro interno das pernas do snorkel, vazão de argônio do liftgás, pressão atmosférica e pressão interna do vaso.
Nessa tabela, será possível alteração dos dados destes parâmetros, para que seja possível comparar cada uma das situações de acordo com o seu tipo de vaso e suas variáveis do processo, visando principalmente conhecer o comportamento da sua taxa de circulação, a qual pode influenciar tanto no tempo de processo, quanto na qualidade do produto final e/ou segurança operacional do equipamento.
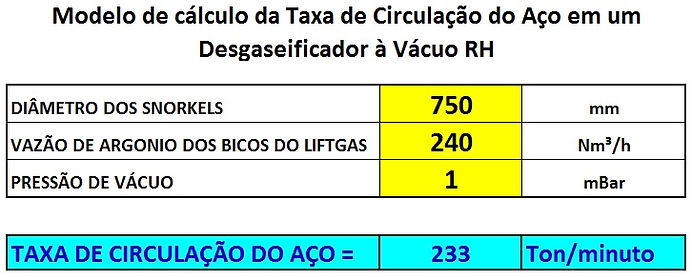
A taxa de circulação do aço através do RH (t/min) desempenha um papel fundamental na cinética de descarburação em função da quantidade de toneladas de aço líquido que circulam pelo vaso por minuto, como decorrência da referida diferença de densidade aparente do aço entre as pernas de subida e descida.
